VEHICLE GROUND
by bd
THE SIGNIFICANCE OF GROUNDAlthough often taken for granted, "ground" is
one-half of every automotive electrical circuit and imposes importance that is equivalent to those of the power source, wiring, wire connections, electrical controls, and components.
For electrical systems in general, 'ground' is defined as the systemwide reference of zero potential, zero voltage, zero electrical energy. In a real sense, ground is the baseline within any given electrical system on which every electrical component relies in order to function correctly.
All meaningful electrical energy and work comparisons depend on ground. Circuit voltages are specified or measured relative to ground, hence, voltage is either positive, zero or negative relative to ground (that is, above, equal to, or below
zero electrical potential). Ground connections must be perfect! Any error occurring in the ground baseline broadly compromises electrical function.
Essentially, it is the controlled, hence, the predictable divergence of voltage away from zero (ground) that makes electricity usable. In other words, as voltage powers an electrical device, all of the voltage applied across that device is used such that zero voltage remains with respect to ground.Automotive electrical systems possess a single ground reference, sometimes referred to as earth. Within specific contexts, ground also is referred to as chassis, common and earth. On a broad scale, ground is considered fully comparable to the electric potential of the body and mass of our planet Earth ꟷ defined as zero and assumed to be unvarying through time. Traditionally, ground is the power source (battery, generator, alternator) return electrical conductor, defined as and assumed to be zero, that is the metallic frame and body (chassis) supporting, surrounding, and shielding the various components and circuitry of the vehicle's electrical system.
Virtually all vehicles manufactured since the mid–1960’s use negative polarity ground systems. As a result, measured voltages are generally zero or positive relative to ground. Bear in mind, however, that from manufacturer-to-manufacturer there are no assurances that the system ground is, in fact, the negative side of the power source. Therefore, when in question, it is prudent to verify ground polarity through direct observation and measurement.
To help alleviate the development of ground errors in aging microprocessor equipped vehicles, beginning in the early 1990's, General Motors medium and heavy truck divisions abandoned using the metallic chassis and bodies of their vehicles as the universal ground path in favor of dedicated ground cabling that connected directly to the negative terminal of the battery. Thereafter, GM considered appliances to be properly grounded only if and when they were effectively connected directly into the network of ground cabling.
HIDDEN INFLUENCES OF "FLOATING" GROUNDSConsistently flawless and uniform ground connections are crucial to the proper function of
every electrical system. Occasionally, electrical systems suffer from unwanted multiple ground levels that are not uniformly zero. For example, the ground bus for a sub-circuit or network of sub-circuits can serve as a "proxy" or "false" ground if it is
above or
below the primary system ground due to electrical isolation from the ground reference terminal of the power source (which is true zero). Such isolation results when a poor intermediate connection exists in the ground bus
somewhere between the sub-circuit(s) and the ground terminal of the power source. Non-zero ground levels are said to "float" above or below ground. 'Floating grounds' are universally undesirable! Electrically energized components connected to a 'floating ground bus' may seek alternate return paths to B- through the non-energized components that are paired with (share) the 'proxy' ground. In other words, circuits backfeed. The resulting symptoms are senseless, unpredictable and often quite wild!
Floating grounds can occur from errors in (re)assembly or develop over time from loose, broken, burned or oxidized connections within the ground path. They typically produce bizarre symptoms that, at first encounter, can be difficult to rationalize and diagnose. Under the right circumstances, floating grounds test the patience of even the most seasoned electricians. Weird, inexplicable combinations of lights, wacky gauge indications when electrical appliances are switched ON, completely inoperative electrical equipment, and electrical appliances that
randomly operate when switched OFF are telltales of floating ground problems. One light dims while another brightens; relays randomly buzz and click; the dash lights illuminate when the wipers are switched ON yet the wipers don't work; turn signals illuminate dimly but don't flash; dash lights dim when a door opens — the irrational combinations of symptoms are endless.
Resolutions to floating ground problems become easier with experience and familiarity with factory ground locations. Patience is key. Ultimately, the solution to floating ground issues is routine and methodical:
study the relevant wiring diagrams as needed, based on which appliances are affected, to systematically locate and repair the offending ground connections.SERVICING THE GROUND PATHNever take an electrical system ground connection or pathway for granted! The importance of good ground connections cannot be overstated! Impaired ground paths cause a myriad of bizarre symptoms when quasi-energized circuits haphazardly function due to unpredicted, substitute ground paths. Faulty grounds can be responsible for mysterious engine shut-downs and random “Check Engine” light activity on electronically controlled engines or random illumination of the instrument cluster turn and high beam indicators when the horn button is pressed. Perhaps the wipers stop working on the high fan setting of the heater blower. Such bizarre and intermittent symptoms always suggest a poor ground — not as an assurance, but statistically!
General service considerations:Star washers promote corrosion between a grounding surface and its connected terminals by decreasing the surface area of contact while allowing moisture, dust and salt intrusion. Hence, star washers should be avoided at any connection carrying three amperes of current or more. Specific connections to exclude star washers are blower motor ground, alternator ground, engine block ground, engine-to-cab ground, frame rail grounds, radiator support grounds and starter motor connections. Star washers in such circuits should be removed and discarded then the connecting surfaces cleaned, burnished and coated with antioxidant as specific problems are addressed.
Except at the starter motor, a hardened steel flat washer may be used between the heads of bolts and ring terminals. The outside diameter (OD) of the flat washer should be the same OD or slightly larger than the OD of the terminal(s). Split lock washers may be used between the bolt heads and the flat washers. On starter motors, ideally, a shoulder-nut (aka, flange nut) should bear directly against the terminal ends slipped over the large battery cable stud of the solenoid.
For general purpose soldering of electrical splices and/or terminals use 0.028" - 0.040" diameter 60/40 (Sn/Pb), 63/37 (Sn/Pb), or 70/30 (Sn/Pb) rosin core solders, ONLY. To repair/resolder rigid printed circuit board foils and through-hole component solder joints that have sheared from standing wave vibrations substitute 1% - 7% silver-bearing (Sn/Pb/Ag or Sn/Ag) rosin core solder to take advantage of its increased shear strength.
To effectively insulate and seal bare electrical splices and wire-to-terminal connections, use dual wall, adhesive lined, polyolefin heat shrink tubing (aka, marine grade heat shrink). Be sure to slip the tubing, precut to the proper length, over the wire before attaching the terminal. Shrink the tubing evenly using a heat gun (the safest method), a micro torch adjusted to a low temperature reducing/carburizing (yellow) flame, a match, a lighter or similar heat source.
WORK SAFELY! If using any type of open flame, be very careful of flammable vapors and materials that are in close proximity to your workspace! Move the flame continuously to prevent scorching of the tubing or wire insulation. Allow at least three minutes of cooling time before handling.Replace Scotch-Loks
® with properly crimped, soldered and shrink-sealed splices or substitute suitable modular terminals that are housed in molded connectors. The ID of ring terminals should closely match the OD of attachment hardware just as mating slip-fit terminals should be correctly matched in size. Replace all broken, deformed or improperly sized ring terminals using bare, plated (tinned), heavy-duty copper or brass terminals. Strip, clean as necessary, mechanically crimp and then solder stranded wire to the bare terminals. Once cool to the touch, insulate the terminal shanks, overlapping the wire insulation, using marine grade heat shrink. Inspect ring terminals for mispositioned insulation or adhesive residue that partially shrouds or covers the clamping surfaces of the ring and trim accordingly.
Always place the ring terminal carrying the greatest current closest to the ground source (which generally should be located at the base of the junction). Or, if all circuits support roughly equivalent current loads, place the ring terminal with the largest outside diameter (greatest surface area) closest to the ground source (base of the junction). Grounding surfaces should be clean, shiny, bare metal. Ground connections between dissimilar metals or those exposed to weather or corrosive environments should be liberally coated with a high-quality antioxidant paste, such as Truck-Lite NYK-77 compound, Gardner Bender Ox-Gard, or thick white lithium grease to help reject moisture and salt and retard electrolysis and corrosion.
Should a ground bus simply become overburdened by current flow, the only solution is to augment the ground path with additional or upgraded cabling and connections. In some cases, this means increasing cable size. In other cases, it may mean reorganizing the sequence of ring terminals within the stack and/or increasing the number of ground attachment points. Still, other cases may require reforming or replacing terminals to correct terminal distortion or improper sizing. For example, the
maximum combined voltage drop allowable across an alternator charge lead and the ground bus is 0.5 volt when the current output from the alternator is at maximum. If an upgraded alternator with increased current output capacity is installed on a vehicle, both the alternator charge lead
and the alternator ground lead, if used, may require replacement with larger gauge cabling to handle the additional current flow. Otherwise, the alternator’s output voltage may be consumed by the cabling and the batteries will charge no better than before the alternator was upgraded.
Another example: the individual connections and wiring within a ground system may be "independently" perfect. Yet, when the individual ground wires are assembled into a column of ring terminals stacked under a bolt or screw, current flow can become opposed by cumulative resistance if the effective cross-sectional area anywhere within the column of terminals or between the column and the point of connection to the ground bus (chassis) becomes inadequate. The result is a 'floating ground' with a portion of the system voltage consumed and wasted across the shared attachment point and/or any alternate ground path that occurs. One possible solution is to reorganize and distribute the individual wires amongst multiple ground attachment points while ensuring that the rings are properly sized, flat and undistorted to eliminate unwanted gaps between rings. Remove any star washers encountered.
Another example: a 10-amp air control solenoid for bags shares its ground attachment point to the cabin sheet metal with the instrument lamps. Now, every time the bags are charged or emptied, the instrument lamps glow dimly. The cause? A poor connection creating a 'floating ground' that backfeeds the instrument lamps. Why? The ground attachment is overtaxed by improper stacking of the ground terminals; although both rings are sized for a #8 screw, the large OD heavy-duty ring for the solenoid is stacked on top of the small OD ring for the instrument lamps; a factory star washer sits between the small ring terminal and the cabin sheet metal. A workable solution is to reorganize the order of ring stacking and burnish the cabin sheet metal attachment point to shiny bare metal such that it matches the larger OD of the heavy-duty ring. Reassemble without the star washer and add a liberal coat of antioxidant paste.
Essentially, as the current load on a system or sub-system is increased effectively beyond its original design capacity, such as by upgrading or adding appliances that increase current flow, or from stacking too many ground wires onto a single attachment point, or by feeding too many subordinate grounds into an overtaxed common bus, the system must be adjusted and upgraded adequately to compensate for the increased demand.
Specific service considerations:Thoroughly burnish and clean the battery cable connections! Employ a specially configured battery terminal brush (image) to service conventional post style connections. Avoid applying acid neutralizers directly to or around the battery. Acid neutralizers consist of chemically active bases that leave conductive residues nearly as damaging as the acidic battery electrolyte. Instead, substitute clear water and a nylon bristle brush to wash away accumulated dirt and corrosive films. Be sure that battery caps are fully installed before and while cleaning the battery! Check for proper torque of cable attachments and remove any paint or corrosive salt encrustations. Check for uneven solder accumulation on all of the battery cable terminal ends. Scrape, sand or buff away excess solder accumulation to ensure clean, uniform, flat, or otherwise conforming clamping surfaces.
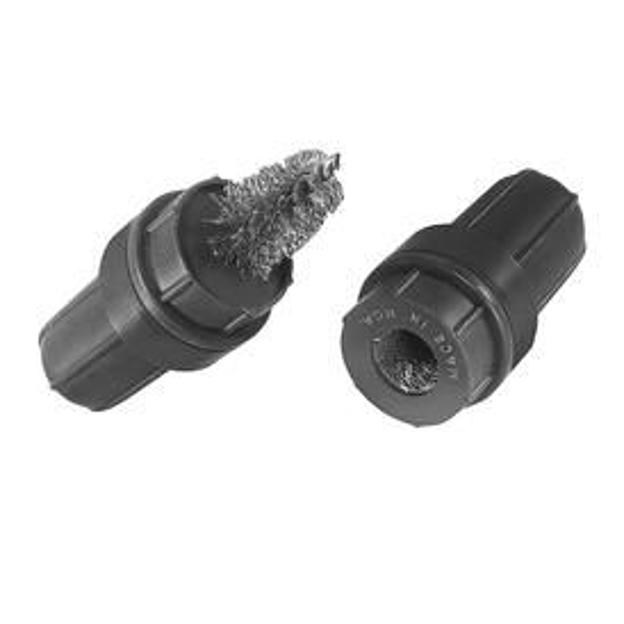
Inspect for star washers, loose connections and corrosion wherever battery cables are fastened to a battery disconnect switch, relay, junction block or the starter. Check for large diameter star washers at the engine block ground stud or bolt. Discard any star washer(s) encountered then thoroughly clean, burnish, assemble and coat the connections with a good antioxidant paste.
Check the tightness and integrity of all connections to cab ground points on both sides of the firewall. Remove any star washers discovered and service the connections as required, coating them with a high-quality antioxidant paste.
STANDARD INVENTORY OF 1973 - 1987 (91) C/K/R/V LIGHT-DUTY TRUCK GROUNDSReiterating, the purpose of the primary ground bus is to ensure that ground is “zero” everywhere in the vehicle. To that end, all subordinate ground buses that feed into the primary ground bus must be at the same ‘zero’ potential. If the ground reference isn't consistently zero throughout the vehicle, matching exactly the potential at the battery ground post, all manner of ill will can result. You'll believe the vehicle is haunted!
Good grounds are vital!Voltage drops across circuit ground paths while the circuits are operating should measure virtually zero. This is true for all low- to medium-current ground wiring (<30 amps). Perform a comprehensive inspection of wire condition and wire-to-terminal connections. Oxidized or frayed wiring should be cut back, cleaned, re-terminated and soldered - or entirely replaced, terminated, soldered and shrink-sealed using marine grade heat shrink as needed.
Whether you are experiencing electrical problems or refurbishing the vehicle, take an inventory of all of the vehicle grounds and service them appropriately (disassemble and clean connections to shiny bare metal, followed by liberally coating terminals and connections with moisture rejecting antioxidant paste). Upon inspection you should discover the following vehicle grounds; recommended wire sizes are listed for any ground paths that need to be fabricated and installed:
- battery-to-engine block or alternator bracket (2 gauge) — this is the primary high-current ground path (>150 amperes) for the engine and cab, supporting the full burden of the starter cranking current, charging system current and cabin electrical appliance current. DO NOT attach the battery ground cable to an intake manifold bolt or stud! Manifold bolts tend to loosen gradually following repeated engine heat/cool cycles as manifold gaskets compress and lose elasticity.
- battery-to-right (passenger side) frame rail (10 gauge) — this ground path is crucial as the primary extension of the main vehicle ground to the rear of the vehicle
- battery-to-radiator support (10 gauge) — this is the primary ground path in support of all of the forward running lamps, forward turn signals, headlamps, and horn(s)
- back of right cylinder head-to-cabin firewall (5/16" braided strap or 8 gauge) — this primary ground path ensures the cabin is adequately grounded in support of all cabin mounted interior and exterior electrical appliances. DO NOT attach the cabin ground cable to a valve cover or intake manifold bolt or stud! Valve cover and intake manifold bolts tend to loosen gradually following repeated engine heat/cool cycles as gaskets compress and lose elasticity.
- dash lighting and interior appliances-to-cabin left kick panel sheet metal (various, but typically 18 and 16 gauge) — this shared grounding point, common to nearly all of the electrical appliances inside the cab, interior lighting and instrument panel, is crucial to preventing the occurrence of floating grounds and associated electrical ghosts.
- rear lamps-to-bed (16 gauge) — ensures the rear lamps are suitably grounded; alternatively, ground the rear lamps directly to the right frame rail
- bed-to-right frame rail (14 gauge) — ensures the bed is suitably grounded in support of the rear lamps and other appliances grounded to the bed
- cabin firewall-to-engine compartment hood (1/4" braided strap preferred for superior flexibility, otherwise 12 gauge, suitably located with sufficient length to allow opening and closing of the hood without catching, excessive flexing or stretching of the wire) — (optional yet highly recommended) helps manage radio "bzzzzzzz" and provides a stable ground for an optional hood mounted engine compartment lamp
Additional primary ground connections are okay. However, if any of the recommended ground connections are missing, fabricate and install them post-haste! If damaged, repair, rebuild or replace them!
(continued below...)